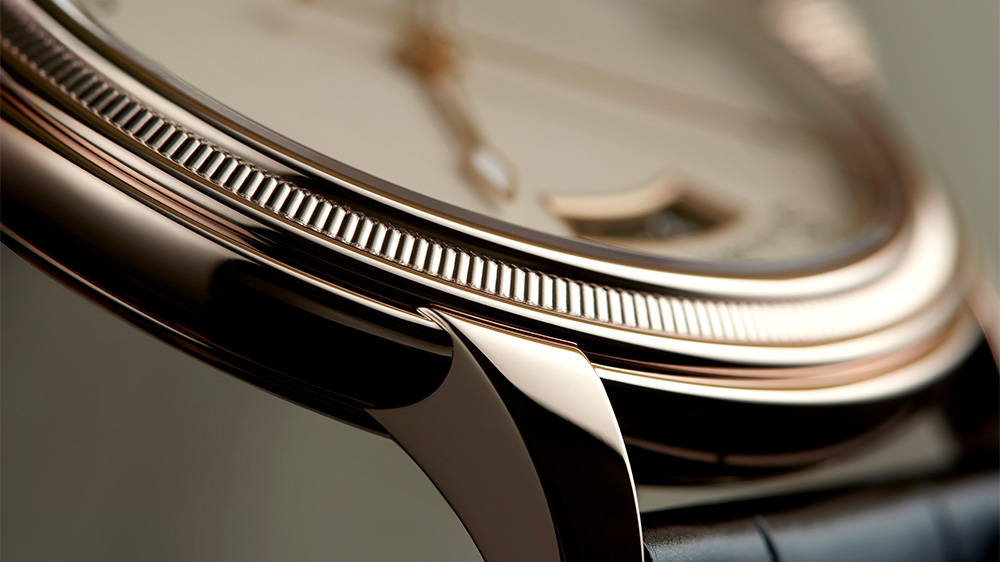
Parmigiani Masters the Art of Knurling
One of Parmigiani Fleurier’s signature details is the iconic knurled bezel of the Toric Collection. This decorative feature was first seen on Michel Parmigiani’s original creation for the brand – a watch he imbued with a classic, timeless design, modelled on the bases of the ancient Greek columns that inspired his first concept. Whether single or double, the concentric relief pattern of knurling enhances the piece by drawing the eye towards the heart of the timepiece.
Since the brand’s creation in 1996, Michel Parmigiani has worked with the same artisan who applies the knurling to every single Toric watch by hand. Through his creations, the brand helps to keep this precious skill alive.
Steady Hand: For this process, the case is held in place by a gripper mounted onto a lathe. The artisan brings the tempered steel wheel, which he has created with the desired pattern, into contact with it, applying just the right amount of pressure. He must take the wheel round the case a hundred or even a thousand times to successfully create a perfect knurled design. This depends on the material to be forged — silver is softer and more malleable, whereas steel is very hard. It also depends on the width and complexity of the pattern being created. When the knurling is more spaced-out, more pressure must be applied.
Although the general theory is easy to understand, the skill itself is incredibly subtle: it cannot be explained, it can only be felt; it cannot be taught, it can only be passed on. By way of an indication of the mysteries inherent to this craft, the number of indentations knurling will produce is impossible to guarantee. Even if we calculate it scientifically and divide the circumference by the width of the indentation to the nearest tenth of a millimeter, this number can vary from 139 to 141 from one Toric to another. However, the finish on each bezel is perfectly regular, and it is impossible to tell them apart. Through successive turns of the wheel and the application of constant pressure, the pattern adapts, becoming regular and settling on a number of indentations that remains a surprise.
Therein lies the magic of knurling by hand. If it was carried out using modern high-tech methods — a numerically controlled machine, a software program and a high-precision laser — it would cease to be beautiful: too clean and symmetrical, too perfect in its geometry to be harmonious. Knurling gets its beauty from the unpredictability of the craftsman’s hand; it is perfect precisely because it is not.